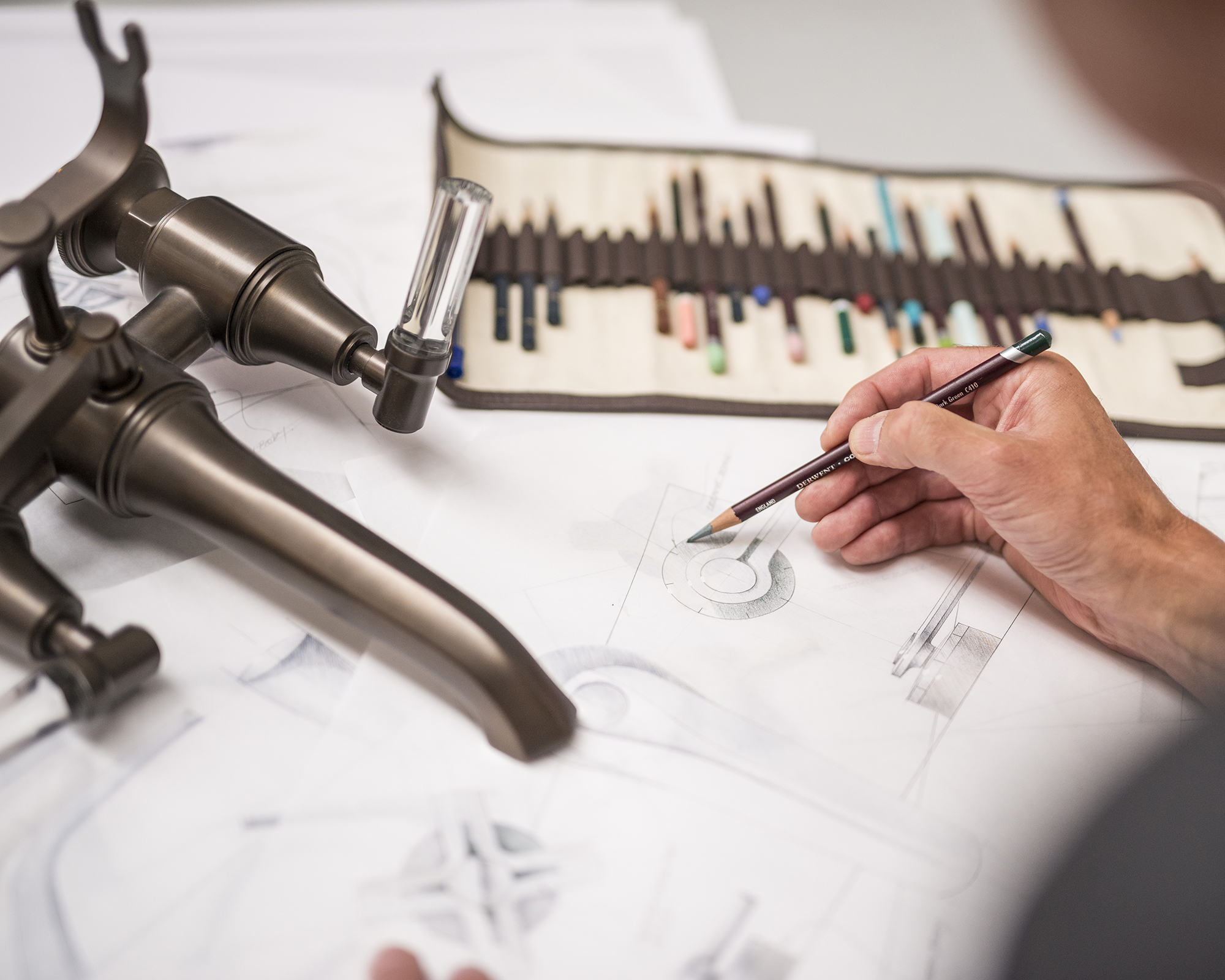
The United Kingdom’s city of Birmingham has long been the home of the country’s metalwork industries with the oldest dating back to the 16th century. Samuel Heath was established in 1820 and is still manufacturing from the same factory that it was 200 years ago.
In the years since it’s inception, Samuel Heath has produced a vast array of products including accessories for firesides, homeware, and giftware. Today, the company draws on their industrious heritage and knowledge of metalwork and brassware to produce the highest quality showers, bath accessories, and door and window fittings, defined by style and performance.
“All of our production processes take place at our Birmingham factory and this means that we have total control over manufacturing, quality, and environmental responsibility,” says Jessica Holmes, digital marketing manager at Samuel Heath. “Our ability to pioneer new movements in brassware is made possible by our unique ability to combine technology tradition and time-honored British craftsmanship.”
While throughout the 1800s Samuel Heath was one of hundreds of brass foundries in Birmingham. Today, it is one of the surviving few.
“We believe that this is because our ethos has changed very little,” says Stephen Hardy, USA National Sales/Specifications Manager at Samuel Heath. “For example, manufacturers may find themselves yielding to the demand for cheaper prices and outsourcing products, we would rather preserve our manufacturing skills, which in turn, allows us to offer bespoke solutions to our customers.”
While a great deal has changed over the years at Samuel Heath, the brand doesn’t compromise on quality of production and a “made-by-hand” approach to all products. The brand also continues to produce entirely from solid brass—a rarity in the industry. This includes internal components often made from plastic, including concealed shower components. And, all products are hand-polished in a different way that machinery simply cannot be programmed to accommodate.
“An inexperienced way of polishing could compromise the grain lines or distort the very malleable metal,” says Holmes. “This kind of skill takes several years to master.”
After polishing, a high-quality electroplating process is applied to achieve a wide variations of finishes. This involves treating the brass in cleaning dips and solutions before further layers of metal plating. These layers of processing are above the industry specifications to retain color and a lasting finish that won’t darken, corrode, or patina.
“Whilst we rely on time-honored British craftsmanship for many of our production processes, we also pride ourselves upon evolving with new movements in bathroom trends and door and window furniture design,” says Hardy. “We continue to invest in state of the art technology, such as CNC machines which adhere to laser-precise details, as well as the brightest design talent in creating the renowned design and quality experience of our products. By coupling traditional techniques with modern processes, we continue to be one of the most trusted, stimulating and imaginative brand for interior designers, architects, and homeowners.”
Samuel Heath will be exhibiting at ICFF May 15-17, 2022.